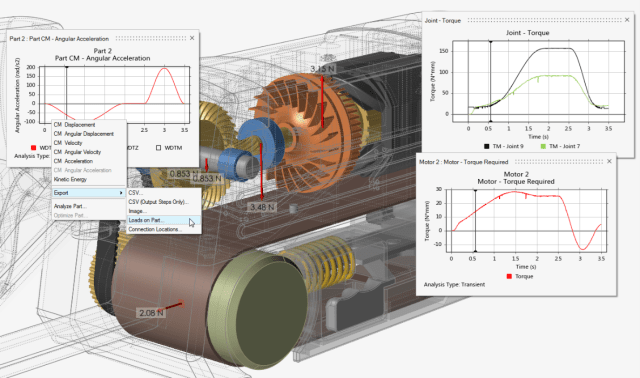
The best product development stories in history were a game of trial and error. To paraphrase Thomas Edison, he didn’t fail to make a lightbulb; along his product development journey he found a bunch of ways not to make a lightbulb. The problem with this approach is that it is time consuming, expensive and clunky to produce prototype after prototype before achieving one that works—let alone one that is optimized. Fast forwarding to modern times, simulation-driven design has become a necessity for design teams looking to produce the best version of their products on the market.
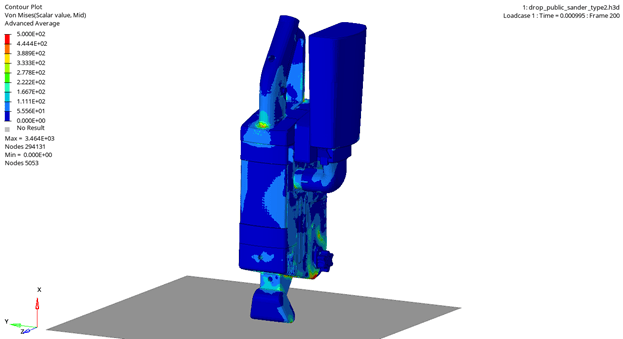
This belt sander drop test simulation, run on Altair Radioss, performed significantly fast on the AMD EPYC 7003 Series processors with AMD 3D V-Cache technology. (Image courtesy of Altair.)
While simulating products early in development, engineers are better equipped to assess a product’s quality, manufacturability and effectiveness before a physical prototype hits the shop floor. The more simulations the team performs, the more likely they will predict defect rates, revenue, warranty costs—and more—early in development, while also optimizing the product and getting to market faster.
“With simulation-driven design, you will have a shorter lead time as you will not have to go through these loops,” said Ujwal Patnaik, Global Business development manager at Altair, at a 2021 conference. “You quickly run [what if] scenarios, you don’t have to wait until the end. You can run these scenarios and improve.”
As a result, to remain competitive, companies are using new software and hardware tools to increase simulation throughput and model fidelity while keeping operational costs at a minimum.
A recent hardware example comes with Altair’s collaboration with the launch of the AMD EPYC 7003 Series processors with AMD 3D V-Cache technology. “We believe our users will achieve great improvements from this enhanced processor, accelerating product development and enabling faster time to solution,” said Eric Lequiniou, vice president Radioss Development and Altair Solver HPC.
How Software Can Increase Simulation Throughput
In his presentation, Patnaik outlines these six common applications of simulation in product design:
- Aesthetics
- Concept design
- Ergonomic design
- Design for manufacturability
- Design for function
- Reliability of design
He noted that by choosing the right simulation software for each step, engineers are better able to perform those assessments quickly. However, he is talking about not only choosing the right software based on its function—which is obvious—but also when that software is intended to be used in development.
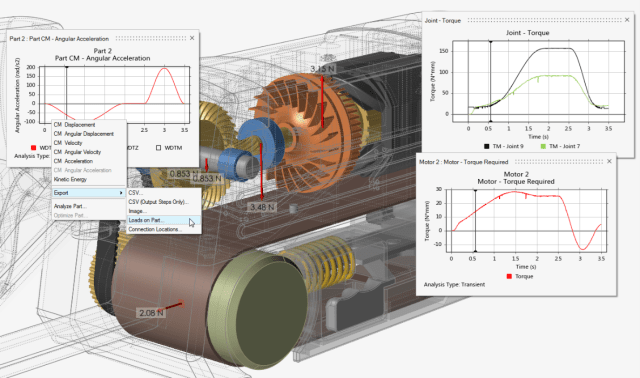
Choosing the right software for the job, and the current step in the development cycle, will speed up a product’s time to market. (Image courtesy of Altair.)
For instance, tools that are optimal for use early in development tend to offer fast results and user interfaces that can easily modify designs on the fly. These tools can assess many potential designs quickly in an effort to guide the designer toward a more optimal design path. Many of Altair’s software options that fall under this category are a part of the Inspire family. Each Inspire tool is specialized to perform specific development assessments very quickly. They also offer a similar user interface, which brings continuity and compatibility, making it easy to pick up one once you learn another.
“Inspire [helps engineers] make better design decisions with a simulation driven design approach,” says Patnaik. “It is a team collaboration tool that offers quick evaluations and rapid convergence.”
Some tools used during this time of development, such as Inspire, are also able to generate potential solutions and models for the engineer to consider. This is called generative design; the engineer tells the software the requirements of a design, its design space and its loads. The software’s algorithms then come up with a working model.
Later in the development cycle, after tools such as Inspire have whittled the design options down to a small few, it is time to perform more heavy-duty simulations. Though these software options run more slowly, they are designed to validate the product’s design. So, the closer you are to an optimized product, and the fewer models you are considering, the less time this process will take.
Patnaik noted that one such tool for this in-depth analysis is SimLab. Although it can be used for optimization, its primary use is to refine and verify models. “It’s also an automated multiphysics workflow that offers fast analysis with optimization,” says Patnaik.
Patnaik suggests that using software with similar workflows and user interfaces can help cut development time, because engineers spend less time learning and relearning tools. However, as long as the software options of choice play well together, it is best to use whichever tool is preferred by the development team for a particular step.
However, software selection is not the only way to improve the throughput of simulations during the development cycle. The Altair team notes that hardware can also play a key role.
Choosing the Right Processor for the Job
To ensure engineers are working on optimal hardware, Altair regularly performs benchmark testing on the latest HPC systems and technologies. A recent example is the 3 rd Generation AMD EPYC processors with 3D V-Cache technology.
Using a server equipped with the new chip, engineers at Altair ran a series of simulations of a realistic belt-sander concept design. For comparison, they also ran it on the chip’s previous iteration, the dual-socket AMD EPYC 7003 and a standard workstation with eight cores.
Both server chips have 64 cores. The major difference between them is the 3D V-Cache technology, which provides each core with 768 MB of L3 cache, giving each core a total cache of 804 MB. The previous model had only 256 MB of L3 cache per socket. Both systems also have AMD Infinity Guard, which includes security features that are built directly into the processors. These features protect systems and software from direct hardware attacks as they are booted.
“We observed significant performance gains running our Altair Radioss crash simulation code compared to initial AMD EPYC 7003 Series processors,” said Lequiniou. “This includes a performance boost of up to 1.8x, with an average gain of around 1.3x, depending on the benchmark model size.”

This thermal CFD simulation, using AcuSolve, ran 1.1 to 1.5 times faster on the new AMD processor compared to previous models. (Image courtesy of Altair.)
In comparison to Lequiniou’s stats, a thermal CFD simulation using AcuSolve ran 1.1 to 1.5 times faster on the new AMD processor compared to the previous model. As for the eight-core workstation, the new processor performed 23 times faster when running the drop test simulation. Altair explained that engineers should expect similar results with other simulations.
The high performance of the AMD chips is expected as these chips are designed for workloads like CFD, FEA, EDA and more.