Siemens Xcelerator, Ansys and NUMECA used for racing yacht.America’s Cup is the oldest and most prestigious trophy in yacht racing. To win the competition requires skill, talent, luck—and every bit of technology a sailing team can muster. The Emirates Team New Zealand, which will be defending the America’s Cup in 2024, will be applying fluid dynamics to create the sleekest and fastest yacht possible.
The America’s Cup race is held every four years and pits two sailing teams against each other: one challenging team and one defending team. The defending team is the prior champion from America’s Cup four years earlier—in this case, Emirates Team New Zealand. The challenging team is decided by a series of races that occur in January and February.
The winning team gets to select the race location and write the rule book for the next Cup. This includes both the sailing style and yacht design requirements/regulations for the next competition. In 2021—the most recent America’s Cup—Emirates Team New Zealand faced off against challenger Luna Rossa Prada Pirelli from Italy, which earned the right to challenge after winning the qualifying races by quite a large margin over INEOS Team UK.
The racing occurs over a period of four to six days. Two races occur on each of the first three days and one race on the subsequent three days until one of the teams is the first to reach seven wins. In 2021, Team New Zealand took a decisive victory against the Italian team with a score of 7-3. Consequentially, New Zealand selected Barcelona as the location for the next America’s Cup to be held in 2025.
AC75 Yacht Performance
The yacht design style for the 2024 America’s Cup in Barcelona has not yet been chosen by Team New Zealand; however, the 2021 design is available for inspection. For the 2021 America’s Cup, Team New Zealand—which also won the competition back in 2017—chose the America’s Cup 75 (AC75) design style , which consists of a yacht with the hull entirely out of the water and riding on hydrofoils. Certain aspects of the vessel, such as the overall structure and length of the yacht, had to meet the design standards; however, important design characteristics like the hull shape and hydrofoil profile could be designed by the two competing teams, allowing for potential performance differences depending on the quality of the engineering design chosen by each team. Based on data from races prior to America’s Cup 2021, and the 10 races between New Zealand and Italy that occurred at America’s Cup 2021, the maximum velocity clocked by one of the AC75 class yachts was an incredible 99 km/h.
Keep in mind that this speed is entirely due to harnessing the energy from the wind. No external energy is added from an on-board engine. Not only was the AC75 incredibly fast, but it was also extremely maneuverable—impressive for a boat weighing over 5 metric tons and with a length of 23 meters.
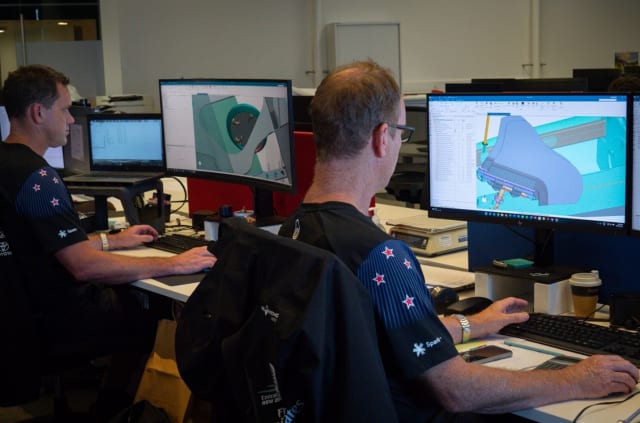
The Emirates Team New Zealand team using Siemens NX and Teamcenter for the design of the racing yacht. (Picture courtesy of Siemens)
The Engineering Behind Racing Yachts
The engineering specifications and design for any racing vessel are of utmost importance. Racing yachts are no exception. The design and manufacturing process of a hydrodynamically streamlined sailboat meant to be the fastest in the world can take multiple years. In yacht racing, there are a few main factors to consider: material composition, wind interaction and water interaction.
Material Composition
In terms of materials, engineers need to consider strength, durability, weight and cost. In the case of a multimillion-dollar racing yacht, the cost of material is not an object. A yacht made of silver and gold may not be race worthy, but the materials used to make these racing craft may be just as valuable.
The hull and mast of Emirates Team New Zealand’s AC75 model was mainly constructed from carbon fiber for its lightweight material, which is also up to five times stronger than steel of equivalent dimensions. The submerged hydrofoils are supported on arms made from carbon fiber and the sails from flexible carbon fiber tape. All told, an AC75 America’s Cup yacht can cost anywhere between $8 million and $10 million to manufacture.
Aerodynamics and Hydrodynamics
The aerodynamics of a racing yacht may at first seem counterintuitive. How can a yacht sail into the wind at speeds faster than the wind speed and yet have no external energy, such as from an engine, applied to it?
NUMECA’s FINE/Marine CFD software was used to design the hull and foils of the ship. The software relies on the Bernoulli Principle, which states that an increase in fluid flow velocity is accompanied by a decrease in static pressure. In addition, conservation of mass means that fluid must travel faster around a curved surface.
How does this impact yacht racing?
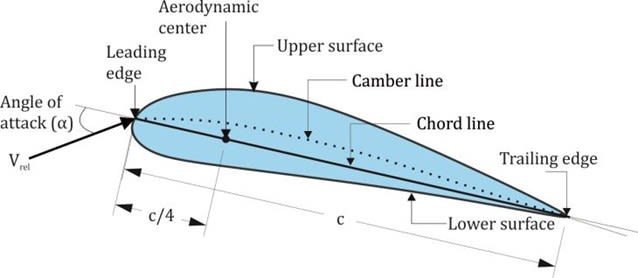
Image of standard shaped airfoil.
Both the submerged hydrofoils and the sails when taut act like the aerofoil pictured above with a curved top surface. From Bernoulli’s Principle, the airflow over the curved surface of the sail causes a pressure difference that results in a directional force in the direction of the convex surface.
This is how racing yachts can sail into the wind. Pointing the yacht into the wind creates a force vector on the sail that pushes the boat forward. As the yacht picks up speed, the air feels like wind. This wind is called apparent wind and in sailing the apparent wind is combined with the true wind, resulting in a force on the sail that produces a velocity of the yacht up to five times that of the true wind speed.
To optimize boat speed, the yacht must be pointed at an angle into the wind rather than directly into the direction of the true wind. The yacht could technically still experience forward motion while pointed directly into the wind.
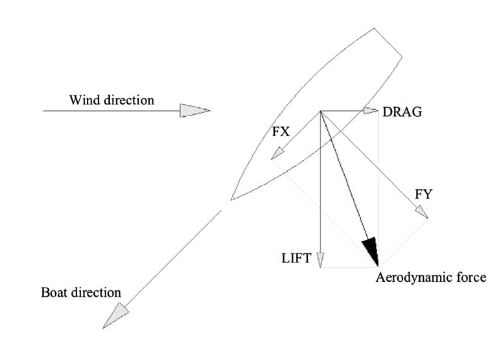
Depiction of the wind forces and interactions on a sailboat.
In the case of the hydrofoils, the experienced lift force is directly upwards. This functions to lift the hull higher in the water and reduces the hydrodynamic drag force. As the yacht picks up speed, its hull will be lifted completely out of the water.
Ansys and NUMECA CFD (computational fluid dynamics) software is used as a simulation tool for engineers to test lift and drag forces on all the yacht’s components. Meshing software will break the 3D model of the yacht into millions of finite elements from which the forces and stresses can be precisely calculated. The air and water will be broken down into millions of finite volumes from which the flow velocity and pressures can be exactly calculated. The interactions of the solid and fluid elements produce an accurate physics model of the entire yacht. This process allows engineers to simulate the yacht’s performance and optimize its design long before it will be manufactured. These engineering tools allow engineers to experiment by passing different air and water flow fields across the yacht.
Siemens’ NX CAD software, integrated with Teamcenter PLM technology, will also be used in the design of the new racing yacht. Together, these tools will act as a single source of truth for the design team.